Have you ever sent out a job that passed your inspection, only to have the customer reject it for out-of-tolerance color? You recheck the data and the instrument says the color passed the agreed tolerance… why is the customer saying it doesn’t? We get a LOT of these conflicting measurement calls in technical support.
The solution is simple – document a color control program that clearly defines how to assess color, then make sure everyone (including your customer) follows it. Today we’re sharing what you need to include in your program so you can begin working with confidence.
1 – Instrumentation
Just because you and your customer both use a color measurement instrument doesn’t mean you’ll achieve measurement agreement. Here are some of the differences you must consider and address.
Type, geometry, and model
Color measurement instruments come in many shapes, sizes, and styles. Colorimeters, for example, are a great way to capture color and do basic evaluation. Spectrophotometers are engineered with three different geometries – 0°/45°, sphere, and multi-angle – for the most accurate measurements.
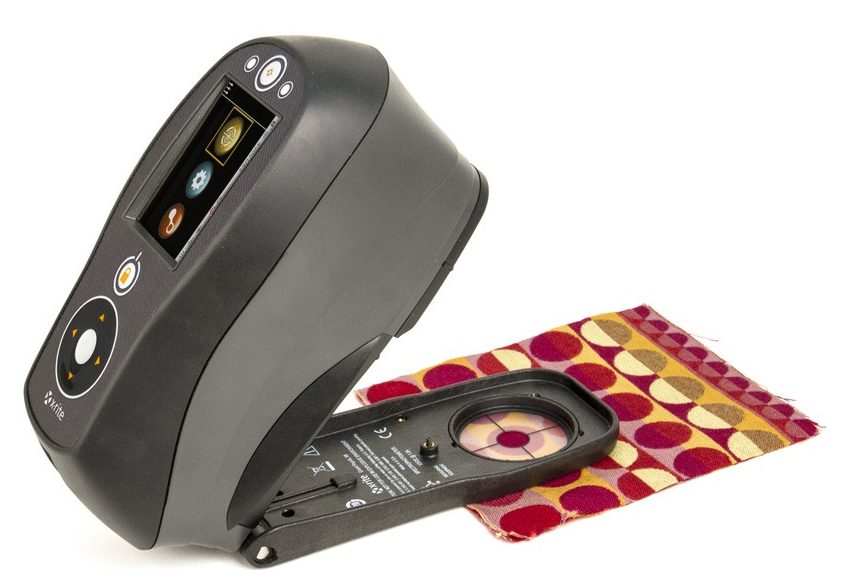
The Ci64 is a multi-purpose handheld sphere spectrophotometer that makes it fast and easy to understand color measurement procedures, ensure consistency, and quickly view measurement data.
Mixing instruments is an issue because they all work a little differently. Even two spectrophotometers of the same geometry won’t measure color exactly the same because of variations in precision. To ensure consistency, everyone must use the same type – and preferably model – of color measurement instrument. Check out these blogs to learn more: What Is A Spectrophotometer? and Colorimeter Or Spectrophotometer: Which Is Best For You?
Aperture Size
All color measurement devices come with an aperture, usually ranging from 1.5mm to 25mm. The size you choose will definitely affect your measurements.
Let’s say you’re measuring a carpet sample that is made with black and white stripes every 5mm. If you use a 4mm aperture, it will make a huge difference where you place it to take the measurement. Your sample could be black, white, or a gray mix of the two. However, if you use a 25mm aperture, you’ll capture all of the colors every time for a more accurate measurement.
Everyone evaluating a color must use the same size aperture, or at least have measurement averaging procedures in place to compensate.
Measurement mode
Various instruments have various measurement modes or settings, and it is critical that everyone uses the same mode. If you are using a 45°/0° instrument, you need to ensure the same M condition is used. If you are using spherical instruments, are you using SCI or SCE, UV calibrated, UV filtered… Again, consistency is the key.
Observer angle
The observer angle setting you choose, either 2° or 10°, will depend on your industry and application. Ensure you and your customer both choose the same one.
Status
Just like your car, you must follow the scheduled maintenance plan to keep your device in good working condition. Regular calibration and routine round robin testing can ensure everyone in the factory is getting the same numbers. It’s also important to send your device for annual certification to ensure it is reading and performing the way it should.
2 – Illumination
The illuminant describes the color of the light under which you’re judging colors. Different industries have different illuminant standards.
This image shows how red and blue sweaters look under four different lighting conditions. As you can see, the type of illumination drastically changes the color. If doing visual evaluation, you must define the illumination settings for the light booth.
You must also specify the illuminant when setting up your spectrophotometer.
3 – Color Calculation and Tolerance
Through the years, different color calculations and tolerancing methods have been developed, which causes a LOT of confusion for suppliers and manufacturers.
Using Lab, there are two calculations to report color difference:
- Hunter Lab (1945) – L a b
- CIELab (1976) – L*a*b*
Using Delta E, there are several:
- FMC2 (1942) – DEfmc2
- Hunter (1945) – DE
- CIE (1976) – DE*
- CMC (1988) – DEcmc
- CIE94 (1994) – DE94
- CIE2000 (2000) – DE2000
To avoid color disagreements, you and your customer must use the same calculation. You also need to make sure you both set your devices to the same tolerance. If yours is set to 2.0 and your customer’s is 1.0, you will be passing color that will fail. You can even set your tolerance a little tighter than the customer’s to cover any variation between measurements.
Here are some tips for defining a pass/fail tolerance for your application.
4 – Measurement Method
Sample Presentation
Many people don’t think about what’s behind their sample, especially if it’s opaque. But choosing (and using) the right backing material is very important because it ensures the device is only measuring the color you want it to.
You must also consider thickness. For example, textile samples are typically folded twice to measure a thickness of 4. Curved or uneven surfaces may require a fixture to ensure consistent sample presentation. Even a variation in pressure can change the result.
However you decide to present your sample to the device, document the method and make sure you and your customer do it the same way.
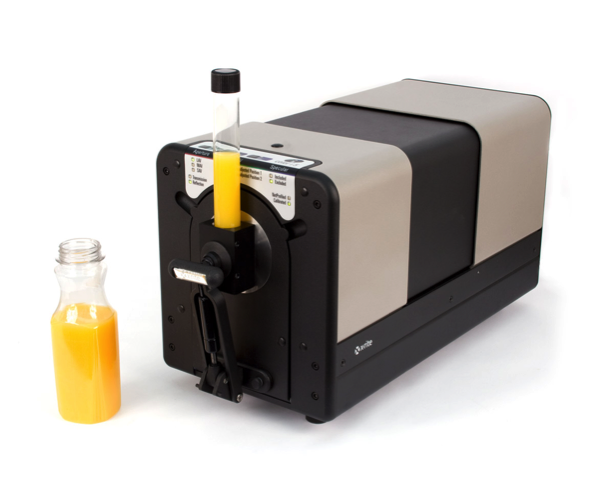
This benchtop spectrophotometer is fitted with a test tube holder to measure the color of orange juice.
Averaging measurements
When you make a pass/fail decision based on a single measurement, you could be capturing the only good (or bad) spot on that sample. We all know the fast pace of production makes it difficult to capture averages, but you need to understand the potential pitfalls if you choose to make decisions on just one measurement.
Standards
While physical standards are a precise way to communicate color, they are also subject to fading, dirt, and damage, which can change the color numbers. You need to store your standards properly – we cover this topic in more detail in our Ultimate Guide for Caring for Physical Samples.
5 – Environment
Temperature
Color is thermo-chromatic, meaning it can change as the temperature changes. One degree Fahrenheit can equal a 0.02 shift in L*a*b* space. That means if you measure molded plastic at 95° in production, then the customer measures it at 72°, you can expect a shift up to 0.46… your pass becomes a fail.
Humidity
Color is also hydro-chromatic. Although humidity typically has a smaller impact, color change can vary depending on the substance being measured.
Drying rate
If you’re working with wet samples, remember that substances dry at different rates. And, as they dry, the color will likely change (think concrete).
Eliminate Your Conflicting Measurements
The best way to achieve measurement consistency is to standardize the entire measurement process. Document everything and share it with your customer.
- Specify:
- Instrument
- Illumination
- Color calculation & tolerance
- Measurement method
- Environment
- Identify each of the variables.
- Get agreement from everyone.
- Test the process.
It really is possible to be confident in your color. Is it worth the time? I will tell you that we rarely get calls from our customers who have established color control programs. Feel free to get in touch for help establishing yours.