If you’re a commercial printer who wants to improve color quality and consistency, this blog is for you.
X-Rite color management solutions for print and packaging deliver excellence in quality control, formulation and automation.
Ray Cheydleur is a printing industry veteran of more than 20 years, a standards guru, and our Portfolio Manager for Printing and Imaging Products. Passionate and very knowledgeable about color, he has a talent for helping printers improve their color quality and consistency.
Today he’s sharing five critical steps in a color-managed workflow to help you create an efficient printing operation, a repeatable final product, and satisfied brand owners.
1. Clear communication and specification.
One of the obvious links in a successful color workflow is clear communication, and a potential key to reducing inefficiencies is digital color specification. Choosing named colors or measuring real-world colors and bringing them into the design provides a solid foundation for the rest of the workflow and delivers a print-ready file that includes spectral color definitions. Even if the color is specified in Paris, printed to the numbers in California, and approved in New York, the digital version of Pantone 360 will always be the same when you use digital specifications across the entire workflow.
2. Measure raw materials.
Since final products are only as consistent as their raw materials, working with a variety of sources can be a challenge. Prior to production, all incoming materials, including ink and substrates, must be measured to ensure expected results. It’s much easier to make recipe adjustments at the beginning of the process than to try to reformulate after color is wrong on the press.
3. Calibrate and profile.
Proofing devices must be calibrated and profiled prior to creating proofs. Presses must be calibrated and either aligned with industry specifications or profiled, and printed output needs to be measured and monitored.
Each time there is a change in supplies or process, you need to either recreate your profiles or correct the situation that created the change. For digital presses, sometimes calibrating the device is enough to keep the profile valid. If you have just performed maintenance or if the media or machine setup has changed, you may need to build a new profile. For analog presses, using a new ink or substrate or starting a new printing condition such as compliance with G7 or FOGRA may require a new profile. But if you meet your standard aims, the ICC profile should remain valid.
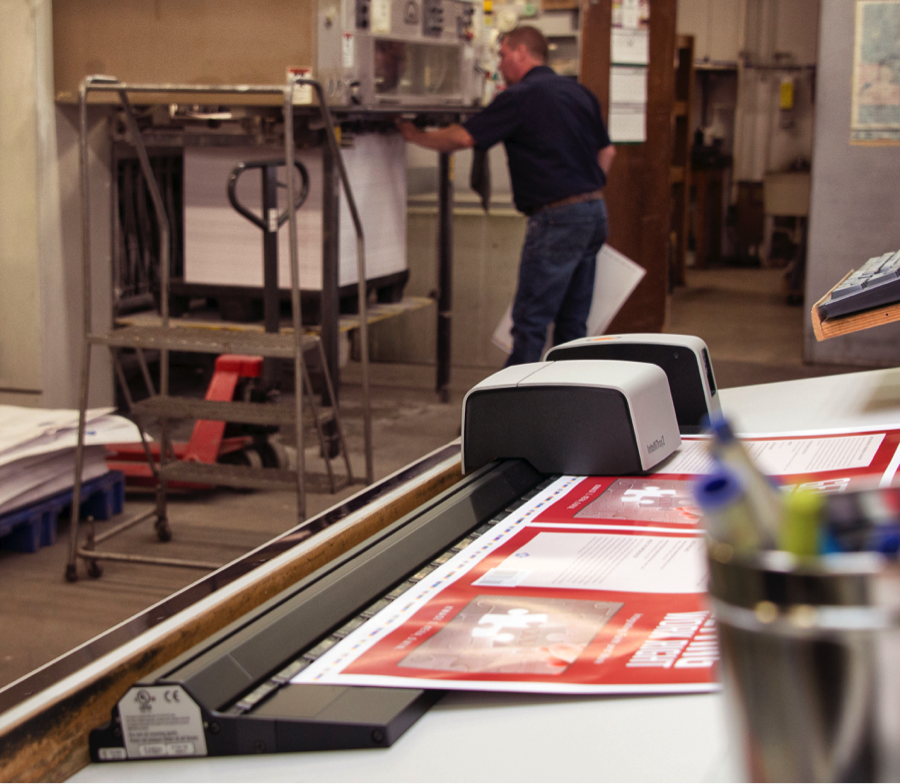
IntelliTrax2 is an automated, non-contact scanning system that makes it easy for busy pressrooms to measure color bars and press sheets without the risk of human error, ideal for high-end, high-speed commercial printing and converting operations.
4. Visually evaluate under controlled lighting.
A light booth provides standardized lighting for proof to print match and can also simulate every lighting condition printed materials or packaging may encounter, from store to office to home. When a finished good is comprised of several materials, such as stand-up pouches, overwraps, and corrugated POP displays, a light booth can also ensure that the harmony among components remains constant under all lighting conditions. A light booth should be used to verify color alignment and to ensure products do not exhibit physical defects.
5. Stay current with standards.
Standards can help you set clear expectations for clients, solve problems in your workflow, and improve productivity. They can also bring an independent perspective to production. Our Staying Current With Standards In Print And Packaging blog provides insight about what’s new in the world of graphic arts standards so you can take advantage of them in your print and packaging workflow.
It doesn’t end there.
Even if you have all the right tools in place, you still need to monitor each step or you’ll spend way too much time trying to fix color issues rather than addressing the root causes of those issues. Make sure you manage the goals you are aiming for – all of them, not just some of them. Especially in an analog shop, it is common to analyze ink density and tone value, but you also need colorimetry and tolerance values as well or you aren’t managing the whole story and may drift out of specification without knowing it.
Whether want to tweak your process for the best outcome or you’re not sure where to begin, our Color Experts are happy to help. Get in touch for custom assistance.
More about Ray
In addition to his role as Portfolio Manager for Printing and Imaging Products at X-Rite Pantone, Cheydleur is also Chairman of the U.S. Committee for Graphic Arts Technical Standards (CGATS), Chairman of the U.S. Technical Advisory Group to ISO TC130 for Graphic Arts Standards, and Vice Chair of the International Color Consortium for Color Management (ICC).