Anyone responsible for printing goods or packaging knows that some colors, like orange, are just too difficult to reproduce using only CMY inks.
A fourth color, black (K, which stands for key color) is often added to subtractive color printing applications. Since C+M+Y actually creates a muddy brownish color due to ink impurities in C, M and Y, adding a true black ink creates the deep color and tones that CMY alone can’t achieve, plus adds density to the shadows.
This four-color printing is called CMYK. Today we’ll look at other ways printers can extend the gamut of CMY to save ink.
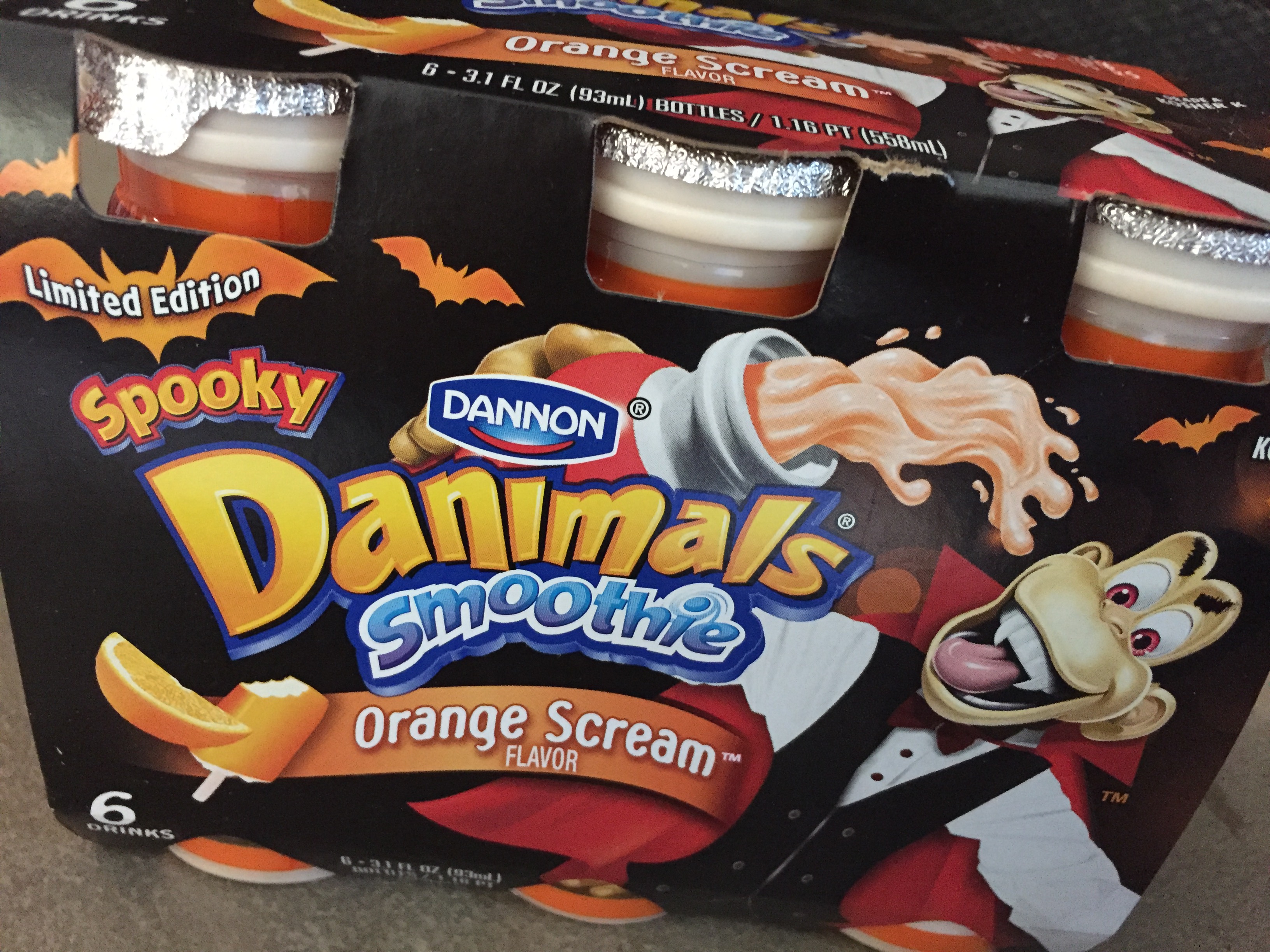
Using gray component replacement (GCR) and spot colors on press can help create a crisper print and more saturated colors.
GCR and UCR
In the 1980’s, a technique called gray component replacement (GCR) was developed. The gray component is the sum of cyan, magenta, and yellow that equals neutral gray. In gray component replacement, the gray component can be partially replaced with black ink. The benefit of using black instead of a mix of CMY is that it adds detail, keeps grays more neutral in various lighting conditions, reduces ink and saves money.
GCR does this for all colors that are comprised of C, M, and Y. Under color removal (UCR) is a variation of GCR that limits the replacement to areas that are nearly neutral and in shadow regions.
Running a press can be a challenge. With multiple ink towers and various press speeds, it can be hard to line up the fine lines of text or images with CMYK printing, or process color. When printing with just black ink, you don’t need to worry about these items being out of registration. Black also adds detail to images. Typically, the more added black, the more neutral prints will appear under different lighting conditions; therefore reducing metamerism.
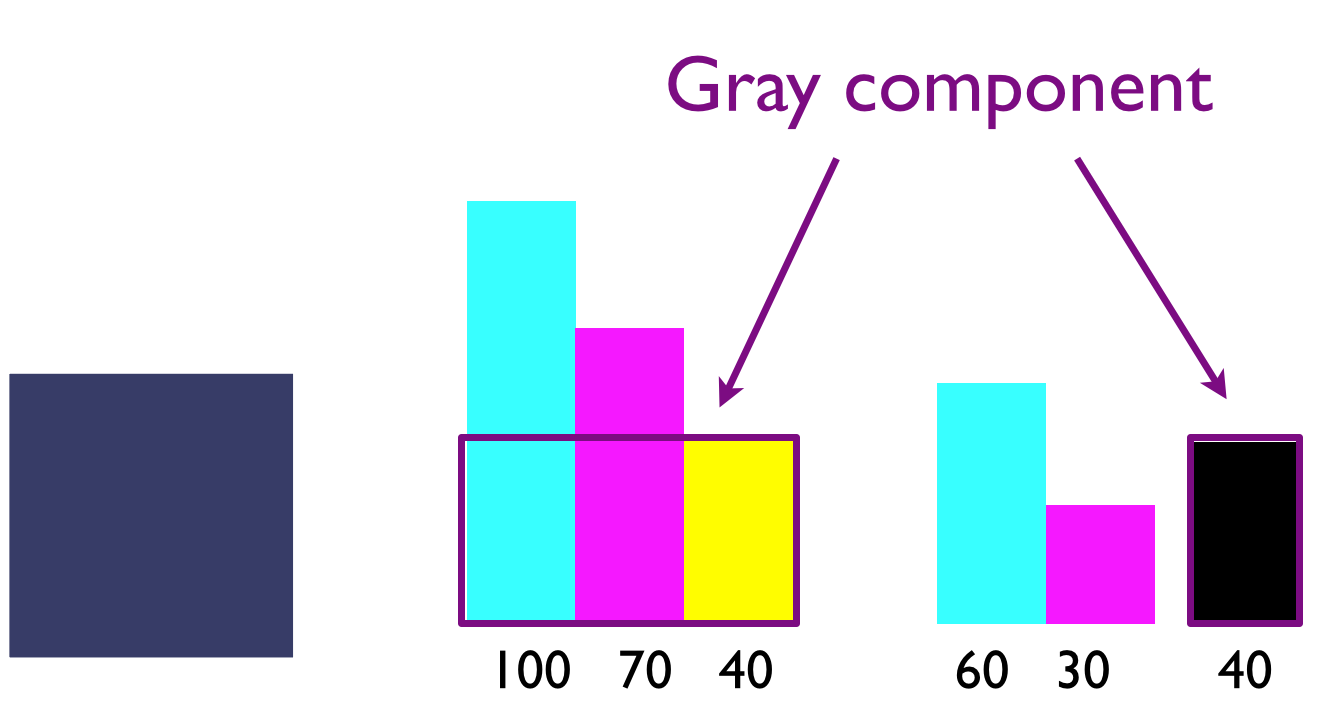
This purple can be built 2 ways: 100% cyan, 70% magenta, and 40% yellow, or take the neutrally equal parts of CMY and replace with black; leaving 60% cyan, 30% magenta, and 40% black.
In CMYK printing, it is often important to limit the total amount of ink laid down in a particular image area. Excessive ink leads to long drying times, smudging, setoff of ink onto the sheet above, and excessive ink usage. When making UCR or GCR separations, the total amount of ink in a particular image area can be quantified as total ink coverage, on a scale of 0-400% – 100% of each C, M, Y and K. Using UCR and GCR, total ink coverage in CMYK printing is typically limited to somewhere between 200 – 320%.
GCR can be set when creating your custom profiles. If you are already using an industry standard profile (e.g. U.S. Web Coated SWOP), the GCR has already been set.
Spot Colors
Colors created without screens or dots, such as those found in the PANTONE MATCHING SYSTEM®, are referred to in the industry as spot or solid colors. They’re commonly used for logos and brand colors or colors that cannot be achieved with CMYK. From a palette of basic colors, each of the Spot Colors in the PANTONE MATCHING SYSTEM is mixed according to its own unique ink mixing formula developed by Pantone®, and placed on a printing unit on the press. These colors are intended to be used on multi-unit presses, where CMYK plus one or more spot color may be printed.
Check out this blog to learn more about getting the best results with Pantone Colors.
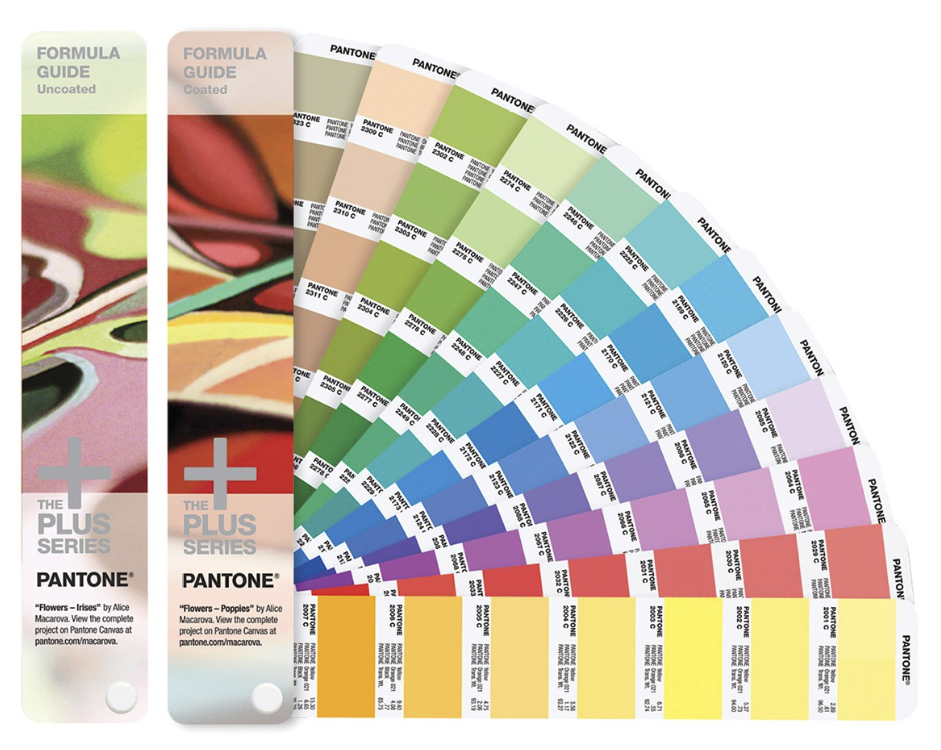
Specification books like these coated and uncoated PANTONE PLUS SERIES FORULA GUIDE Coated & Uncoated fan decks provide ink formulas to help the ink room create each color to be used on press.
Multi-Color Printing
Adding fifth, sixth, or even seventh color to CMYK process printing can extend the gamut and help produce more accurate brand colors than CMYK alone.
The PANTONE PLUS SERIES EXTENDED GAMUT Coated Guide can help you manage these reproduction expectations. Each guide is printed with an extremely high quality, seven-color printing process using existing Cyan, Magenta, Yellow and Black (CMYK) inks, plus commonly used Orange, Green and Violet (OGV) inks to significantly extend the achievable color gamut. With these seven colors, you can accurately simulate most of the 1,729 solid PANTONE MATCHING SYSTEM Colors, including those pesky oranges. To read more about extended gamut standardization, check out this article by Senior Editor Cary Sherburne on WhatTheyThink.
A number of large-format inkjet printers use multiple ink systems consisting of CMYK plus light cyan and light magenta. The lighter process colors enable finer tonal gradations to be printed in highlights with a less conspicuous dot structure. These printers also often use additional inks to extend the gamut, using different combinations of orange, green, blue, red and violet.
Learn More
If you’d like to learn more about this and other printing topics, check out our Color Control Freak eLearning course, or get in touch to speak with one of our Color Experts.